Implementing AI in Manufacturing: A Case Study
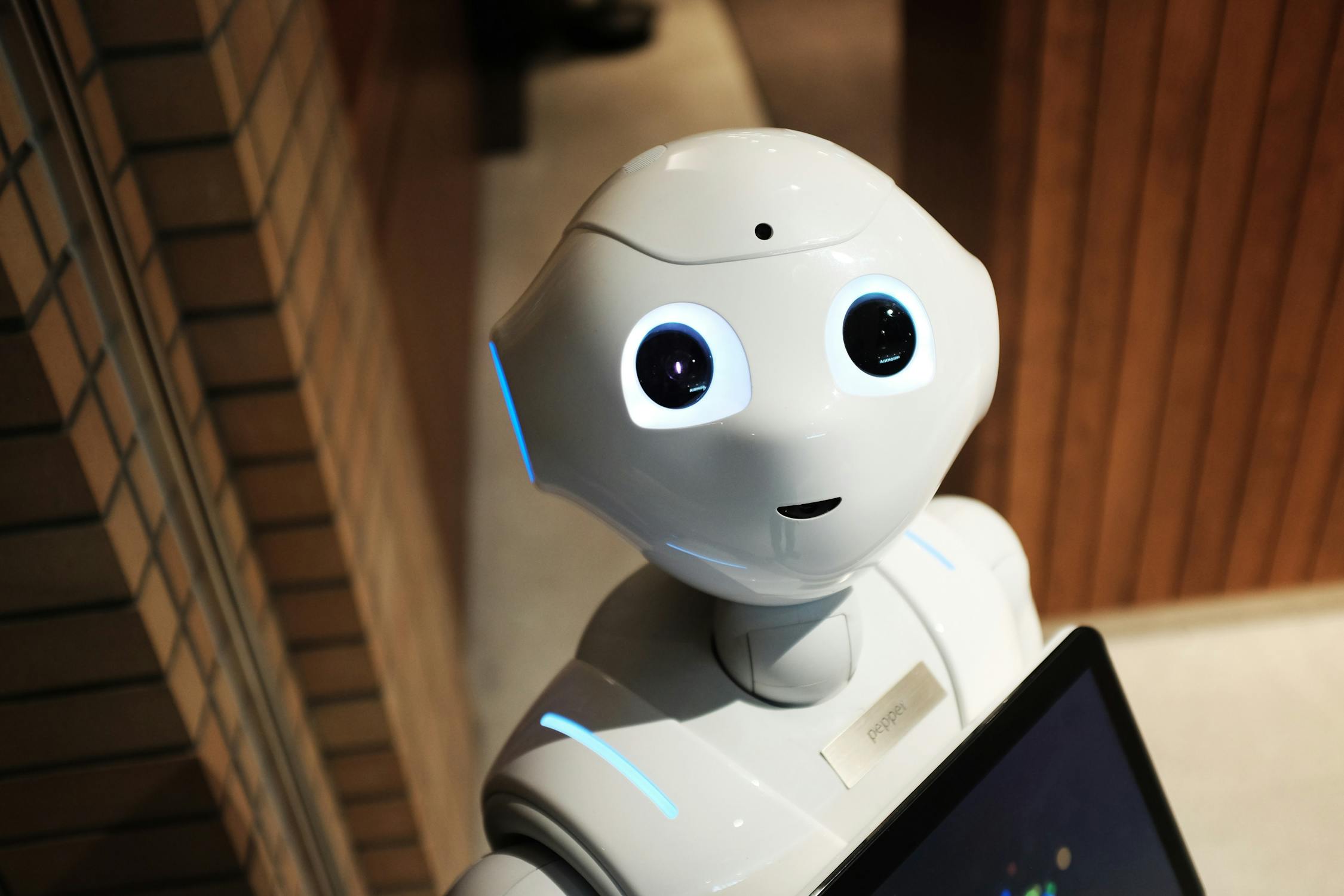
Artificial Intelligence is revolutionizing the manufacturing industry, enabling unprecedented levels of efficiency, quality control, and predictive maintenance. In this case study, we'll explore how a leading manufacturer implemented AI solutions to transform their operations.
The Challenge: Modernizing Legacy Manufacturing
EuroTech Manufacturing, a mid-sized automotive components manufacturer with facilities in three countries, was facing increasing pressure from competitors who had already begun digital transformation initiatives. Their traditional manufacturing processes were reliable but increasingly inefficient compared to more technologically advanced competitors.
The company was experiencing several critical challenges:
- Quality control processes that relied heavily on manual inspection
- Unplanned equipment downtime averaging 15% across their production lines
- Sub-optimal production scheduling leading to missed delivery deadlines
- High energy consumption and material waste
- Difficulty attracting skilled workers to operate in a non-digitized environment
The AI Implementation Strategy
Rather than attempting a wholesale transformation, EuroTech worked with DataMinds to develop a phased implementation approach that would demonstrate value quickly while building toward a comprehensive AI-driven manufacturing environment.
Phase 1: Computer Vision for Quality Control
The first phase focused on implementing computer vision systems for automated quality inspection. High-definition cameras and deep learning models were deployed to inspect components at various stages of production. The AI system was trained on thousands of images of both defective and non-defective parts to recognize even subtle quality issues.
The results were impressive:
- 98.5% defect detection rate, compared to 92% with manual inspection
- 85% reduction in quality control labor costs
- 42% decrease in customer returns due to quality issues
- Real-time data collection on defect types and frequencies
Phase 2: Predictive Maintenance
Building on the success of the quality control implementation, EuroTech next deployed IoT sensors across critical manufacturing equipment to collect real-time performance data. Machine learning algorithms analyzed this data to identify patterns that preceded equipment failures.
The predictive maintenance system generated significant value:
- 73% reduction in unplanned downtime
- 31% decrease in maintenance costs
- 22% improvement in overall equipment effectiveness (OEE)
- Extended equipment lifespan averaging 15-20%
Phase 3: Production Optimization
With quality control and equipment reliability significantly improved, EuroTech implemented AI-driven production optimization. Advanced machine learning algorithms analyzed historical production data, current orders, inventory levels, and equipment status to optimize production scheduling.
The system continuously adapted schedules based on real-time conditions, automatically adjusting to unexpected events such as rush orders or supply chain disruptions.
The optimization system delivered:
- 28% increase in production throughput
- 15% reduction in work-in-progress inventory
- 18% improvement in on-time delivery performance
- 12% decrease in energy consumption
Implementation Challenges
The AI implementation journey wasn't without challenges. EuroTech faced several significant hurdles:
Data Quality and Availability
Initially, EuroTech lacked sufficient high-quality data for training the AI systems. To overcome this challenge, DataMinds implemented a two-month data collection phase, deploying temporary sensors and cameras to gather the necessary training data. This required careful planning to avoid disrupting ongoing production.
Legacy System Integration
Integrating AI systems with existing machinery and software posed significant technical challenges. The solution involved developing custom APIs and middleware to enable communication between new AI systems and legacy equipment. In some cases, edge computing devices were installed to process data locally before transmitting it to central systems.
Workforce Adaptation
Perhaps the most significant challenge was helping the workforce adapt to the new AI-driven environment. EuroTech invested heavily in training programs, emphasizing that AI would augment rather than replace human workers. They created new roles for "AI operators" who would oversee and fine-tune the AI systems, providing career advancement opportunities for existing employees.
Results and ROI
Two years after beginning their AI implementation journey, EuroTech has achieved remarkable results:
- Overall productivity improvement of 35%
- Manufacturing costs reduced by 23%
- Customer satisfaction scores increased from 82% to 94%
- Employee satisfaction improved by 18% as tedious, repetitive tasks were automated
- The company achieved a positive ROI on their AI investment within 14 months
Lessons Learned
EuroTech's experience offers several valuable lessons for manufacturers considering AI implementation:
- Start with high-impact use cases: Begin with applications that can deliver measurable ROI quickly to build momentum and support for broader implementation.
- Invest in change management: The human element is critical to successful AI adoption. Involve workers early, provide comprehensive training, and create new career paths.
- Build data infrastructure first: Ensure you have systems in place to collect, store, and process the data required for AI applications.
- Choose scalable solutions: Select technologies and platforms that can grow with your needs and integrate with future systems.
- Measure and communicate results: Track and share the outcomes of each implementation phase to maintain organizational commitment.
Conclusion
EuroTech's AI implementation journey demonstrates that manufacturing AI isn't just for industry giants. Mid-sized manufacturers can achieve significant benefits through thoughtful, phased implementation strategies that balance technological innovation with practical business considerations.
As the cost of AI technologies continues to decrease and implementation expertise becomes more widely available, manufacturers of all sizes have unprecedented opportunities to enhance their operations through artificial intelligence.
At DataMinds, we specialize in helping manufacturing companies implement practical AI solutions that deliver measurable business results. Contact us to discuss how we can support your AI journey.
Michael Johnson
Manufacturing AI Specialist
Michael has over 20 years of experience in manufacturing process optimization and automation. He specializes in helping traditional manufacturers implement AI solutions that drive measurable business results without disrupting ongoing operations.
More Articles
Ready to Transform Your Manufacturing with AI?
Contact our manufacturing AI specialists today to discuss how we can help your organization implement practical, high-impact AI solutions.
Contact Us Today